Tesla Model 3 Charger/DCDC ("PCS"): Difference between revisions
No edit summary |
|||
Line 79: | Line 79: | ||
# Typical alerts with this configuration (no HV DC battery or charger interface connected) will be: 63chgVOutRationality, 66dcdcHVRationality | # Typical alerts with this configuration (no HV DC battery or charger interface connected) will be: 63chgVOutRationality, 66dcdcHVRationality | ||
# Now the connections and communication with the PCS and controller are established, further testing can be carried out to check DC-DC and charging functionality. See below<br /> | # Now the connections and communication with the PCS and controller are established, further testing can be carried out to check DC-DC and charging functionality. See below<br /> | ||
=== DC-DC First Test === | |||
TBC | |||
=== AC Charging Test === | |||
TBC | |||
The minimum recommended HV DC battery voltage for testing is 250V (This needs to be confirmed) | The minimum recommended HV DC battery voltage for testing is 250V (This needs to be confirmed) | ||
[[Category:OEM]] [[Category:Tesla]] [[Category:Charger]] [[Category:DC/DC]] | [[Category:OEM]] [[Category:Tesla]] [[Category:Charger]] [[Category:DC/DC]] |
Revision as of 16:08, 11 September 2022
Overview
The Tesla Model 3 has a "Power Conversion System" (also known as the "PCS") which contains both a 10kW AC charger and a ??W DCDC converter. The PCS is located inside the "Penthouse" part of the main traction battery system.
Learning/Resources
Video - The Tesla Project : Model 3 PCS First Look - https://youtu.be/_TYvSmDJSPQ
Video - Tesla Model 3 Power Conversion System - https://youtu.be/3ARHdRwfxjY
OpenInverter PCS overview/tech thread: https://openinverter.org/forum/viewtopic.php?f=10&t=171
OpenInverter PCS controller support thread: https://openinverter.org/forum/viewtopic.php?p=27744#p27744
Damien's GitHib: https://github.com/damienmaguire/Tesla-Model-3-Charger
Hardware
Controller
Damien from EVBMW has designed a control solution which is open hardware, but closed software. Design files for the controller hardware are available on Damien's GitHub here. Licenses for the software are available through Johannes' OI webstore here. Controllers are also available as a fully-built kit (with pre-loaded software) on the EVBWM webstore here.
The PCS comes with different firmware versions some of which don't currently work with the above controller. We are in search of a solution.
Data Connectors
EDITOR'S NOTE: my research shows some conflicting/different part numbers mentioned - would appreciate some clarification here once validated
As per: https://openinverter.org/forum/viewtopic.php?p=26614&sid=24f0c02f437aeba37d4fc698d0ce54e6#p26614
The connector used for communications with the PCS :
https://www.te.com/global-en/product-1379662-5.html
https://www.mouser.ie/ProductDetail/TE- ... KwrJA1Y%3D
Pins: https://www.mouser.ie/ProductDetail/TE- ... DUA4Ad4%3D
In true Muskian fashion it seems they use the 1379662-5 natural color variant of the plug which has no coding tabs. It is of course unavailable from mouser. The black and green variants are functionally identical and should work with coding tabs removed.
However, as per: https://github.com/muehlpower/EV-FFB, there is also mention of 1318774-1 (white) or 1318774-2 (black) for the comms/data connector.
Power Connectors
The power-side connector assemblies are not widely available. The housings are a Tesla internal part (photos/part numbers here), however, 3D printable housings have been made available here. The terminals also aren't widely available, but are known. As per https://github.com/muehlpower/EV-FFB:
The contacts for 400V are Uni F630 from MTA, part number 1107940. For 12V Kostal PLK 14.5, part number 23124734300. The connector for the data is from TE connectivity, part number 1318774-1 for white or 1318774-2 for black.
Connections
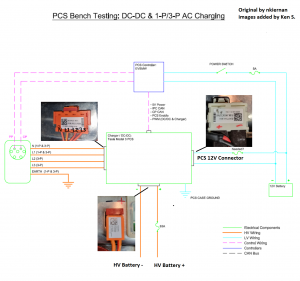
The minimum wiring needed to wake the PCS:
- PCS controller connected to PCS via 12-way X420
- PCS controller is powered via 20-way +12V input pin and grounded to chassis via 20-way ground pin
- +12v and Chassis ground applied to PCS 12v Connector input terminal
- Chassis ground on the PCS case
Firmware
Current Version
The current version of the PCS firmware can be found here: https://github.com/damienmaguire/Tesla-Model-3-Charger/releases
This now includes an integrated alert logging function to help diagnose any issues the PCS sees
Alerts Logging
The PCS has an array of potential alerts to help diagnose issues. The images below show a matrix of potential alerts
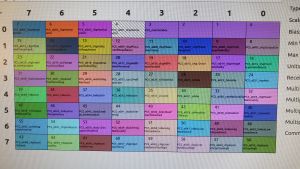
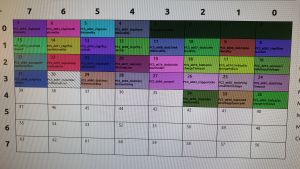
Initially alerts had to be identified through CAN logs (PCS IPC CAN). In later firmware releases, the PCS web interface incorporated a decoder to help identify alerts (decimal number identifier relating to the alert tables shown here). In the current version of firmware, the alerts are now displayed in word format to make it easier and quicker to troubleshoot.
Testing
First Power Up
Set up to initially test connections between a PCS and the PCS controller are straightforward. This can be done without any HV DC battery or charging connected to the PCS. Once the PCS controller is connected to the PCS (follow the relevant V2 or V3 pin-outs) the basic steps are:
- Connect the PCS aluminium case to LV ground
- Connect PCS controller ground wire to 12V ground
- Connect PCS 12V power wire via a 5A fuse to +12V
- Observe the PCS controller continuous 3.3V indicator red LED and the flashing activity red LED
- Connect to the PCS controller wifi to view the web interface. The interface will indicate that the PCS 'opmode' is 'Off' at this time
- On the web interface, change 'inputype' to 'Manual' in the drop down menu and select refresh at the top of the screen
- On the web interface, change 'activate' to 'Both'. This will tell the PCS to try start DC-DC and Charging if enabled (as above, these are not connected at this time so will generate alerts that will be mentioned further below)
- On the web interface, change 'AlertLog' to 'On'. This will tell the PCS to show any alerts
- To enable the PCS connect the PCS controller 'Input 1 (enable)' wire to +12V and select refresh at the top of the screen. 'Opmode' should now change to 'Run' on the web interface to show the PCS is now operational
- At this point, 'PCSAlertCnt' will likely show a number indicating the number of alerts the PCS has flagged and 'PCSAlerts' will show the first alert
- To see each alert separately, under General, change the number in the 'Alert' option (0 indicates first alert and should be default) to the next sequential number and select refresh at the top of the screen. 'PCSAlerts' will now show a description of the selected alert. Do this to step through each alert (total number indicated by 'PCSAlertCnt')
- Typical alerts with this configuration (no HV DC battery or charger interface connected) will be: 63chgVOutRationality, 66dcdcHVRationality
- Now the connections and communication with the PCS and controller are established, further testing can be carried out to check DC-DC and charging functionality. See below
DC-DC First Test
TBC
AC Charging Test
TBC
The minimum recommended HV DC battery voltage for testing is 250V (This needs to be confirmed)