Over the past few weeks and months I’ve slowly been improving the car with battery boxes, newly redesigned HVJB and PTC cabin heating. My knowledge of messing with Arduino code has also improved (although I’m still useless), largely thanks to Jon Volk’s signposting and this has opened up other opportunities to control systems within the car.
With the assistance of a friend we (he) fabricated some stainless steel battery boxes and fitted them in engine bay and beneath the boot floor. They’ve been designed in such a way that the frame system can be dropped out of the car in one piece in about 30 minutes; battery and motor attached; and a minimal amount of unplugging. This is a huge advantage for maintenance reasons. I just need to find some decent quality shut-off valves for the coolant lines so the system doesn’t need to be fully drained each time. I’m also on the hunt for some reasonably priced IP rated HV plugs so that I can easily disconnect the front battery upon removal of the frame system.
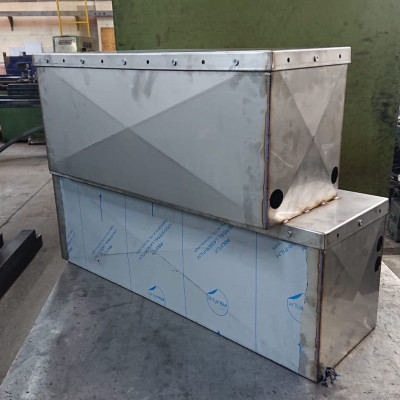
This picture shows the largest of the boxes and the strengthening at the base, which bolts into the frame system below it. Copper battery terminal bus bars were fabricated to reduce the need to contort the HV cables and help when paralleling the packs together (the boxes are rubber lined). We also integrated small bulkhead into the lower box to accommodate the coolant lines. The bottom lid is welded to the box above it.
Unfortunately, during the installation it was unforeseen that that the handbrake cable would not fit around the outside of the battery boxes and therefore a bespoke cable was ordered at a stupidly expensive price – this delayed things a week or so. I took the opportunity to replace the brake shoes at the same time, which complimented the recent service on the drive shafts – new bolts, boots and CV grease.
Lower box in situ with no lid yet to be fitted (The lids attach with M6 bolts.).
This picture shows two battery boxes in situ inside the engine bay. Before production we were careful to measure all of the dimensions accurately and this paid off as there’s about 10mm to spare between the top of the box and engine bay cover. I can categorically say this wasn’t a fluke.
Underneath the car looks like this: The rear box houses the second mid-size battery brick and is welded into the boot floor of the car. I’ve not included a picture inside the boot at I’m still working on the rats nest of OEM LV wiring and waiting for my mini VCU to arrive. The Porsche DME motronic system still needs to see some signals in the car in order for the ignition and auxiliary power management to function, therefore going through the process of depinning and removing the unwanted ICE elements of the car’s harness is painstaking. Trying to make the conversion as clean as possible therefore didn’t want to stuff unwanted wires out of sight and forget about them.

One thing that I hadn’t considered is whether my HVJB would fit in the engine bay after stuffing it full of batteries - It doesn’t in the current form factor, which was a bit of a blow, meaning that I had to knock-up a smaller one, and I spent a whole day doing just that. However, because I’m an idiot, I wired the LV side in such a way that enabled the DC2DC under load before closing the main contactor (and left it like that for about 30 minutes pulling current through the pre-charge circuit) and melted the side of PVC HVJB that the pre-charge resistors were bolted to - I could have cried. Therefore, I’m now onto HVJB V3 with both DC2DC and PTC heating only enabled after the main contactor closes. You live and learn. But hey, at least the DCDC HV is connected on the OEM side of the contactors, right, Arber333?
HVJB V3: